The concept of a circular economy isn’t a revolutionary new concept but one that has been practiced since humans first crawled out of caves. But doing it at scale is the real trick. That’s exactly what BMW and MINI are aiming for with their massive recycling center in Unterschleißheim, Germany. To experience this unseen part of the automotive lifecycle, BMW invited us for an inside look at the plant, the process and even the cars that are ultimately crushed. Oh and we got to blow up some airbags for fun.
The recycling process is all about closing material cycles, extending resource life, and reusing them more efficiently. None of this is new for BMW. The brand has been designing its cars to be easily recycled since the early 90’s – well before any regulations had been put into place. Since then the EU has required any vehicle from 2008 onwards should be reach a recycling target level of 85 percent and a recovery target level of 95 percent by 2015. Luckily BMW has been exceeding that for years and has internal goal of 95% recyclable for all its new cars.

Treasures Were Lurking Everywhere
We first entered the “waiting room” which is a parking lot outside of the plant. While most cars were test mules and pre-production (some with camo included) there were plenty of interesting things to look at. A Rolls Royce Spectre prototype disguised as a 7 Series was the first thing we noticed. Then in the corner was something unmistakable – at least to us. Peaking out from under a tarp was the unique shape of the 2nd generation Clubman concept with its memorable 20” wheels and unique front air damn. Apparently it was one of two that were made for the launch of the F54. But don’t worry, according to MINI the only running prototype has been saved deep in a secret Munich basement. And we did ask if I could buy the car or at least wheels. And naturally I was told no.
Much of what we saw looked intact and almost perfectly ready for the road. However by law BMW can’t sell any pre-production products and thus all must be broken down and recycled. But not all is lost, some components such as wheels are inspected and sold as pre-owned accessories by German dealers.

Batteries and Orange Cords
Our first step inside was the battery dismantling room where a number of hybrid and full EVs were in various states of undress. It’s in this room that BMW technicians safely remove all live batteries destined for their own intricate dismantling and recycling process.
One thing that was fascinating to see was the massive growth in battery size and how the cars themselves have been designed to accommodate them. We all know it on paper but seeing how BMW has engineered cars like the new 7 Series to exist as both an EV and an ICE variant is really astonishing.
From there we entered the main part of the plant where we saw cars stacked to the rafters. It’s here where BMW systematically detonates the airbags and all other explosive safety devices on the car. The process involves a lot of wires, ear protectors and a huge tethered remote with lots of buttons that detonates all those changes. Oh did I mention I got to detonate them? One of the more satisfying things I’ve done in my life.


The Sad End to Beautiful Cars
Everywhere I looked there were interesting cars that felt just wrong to see about to be crushed. A pre-production i8 Spyder in seemingly perfect condition was particularly tough. As was a seemingly perfect MINI Convertible Cooper SE – yes even the highly limited electric MINI convertible meets its fate here.
Unquestionably the star of the touch was the crusher. Yes that thing that turns cars into cubes is real and as alarming and strangely satisfying as you probably imagined. We were treated to a pre-production BMW X6 get turned into a long rectangle of metal and saw what was once a gorgeous Isle of Man BMW M8 in full cube form.
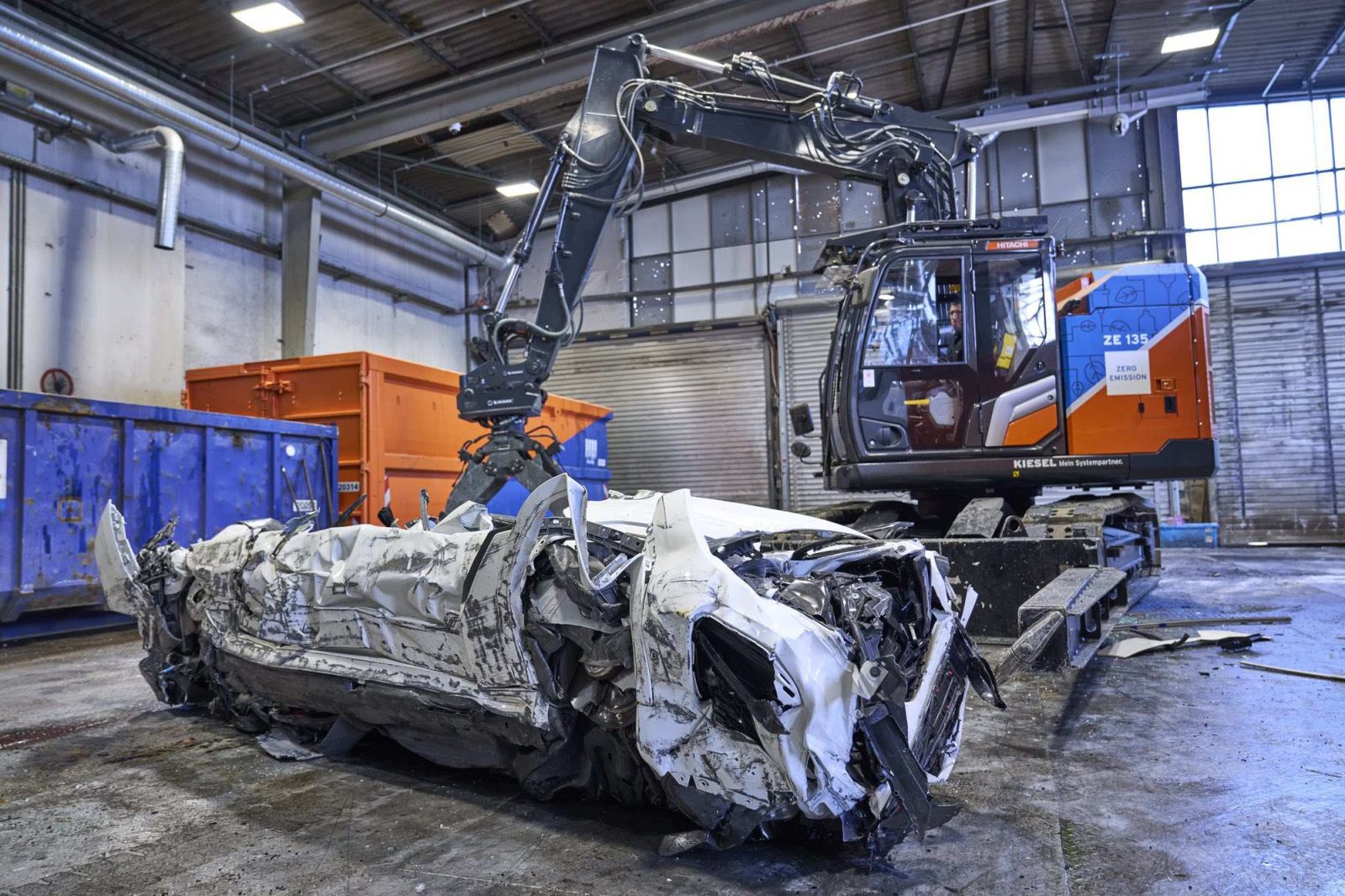
What’s Next
The same type of recycling mandates are also coming to the US. As it stands this is regulated by both the Federal Government as well as the states. Not unlike the EPA and state led environmental laws governing emissions, there are different rules per state. While things are still developing we would guess that progressive states like California will likely mandate a certain percentage of recovery from every vehicle sold in the state. Of course laws like don’t impact normal consumers but it does put pressure on automakers to be responsible in how they design and build their cars.
To that point the vast majority of cars the BMW handles are from their own development processes. A very small percentage are made of consumer dropping off old, unwanted cars.
Where does BMW and MINI go next? There will be an even greater emphasis put on using recycled and easily reused materials in future cars. We already know that MINI will be replacing polyurethane foam with fabric in future models and both BMW and MINI are aggressively moving towards leather free interiors that are easily re-used.
The real challenge will be to see if they continue down these paths without sacrificing the qualities we love about the cars. But given what has been accomplished since the program started in the early 90’s, it’s easy to imagine anything is possible.

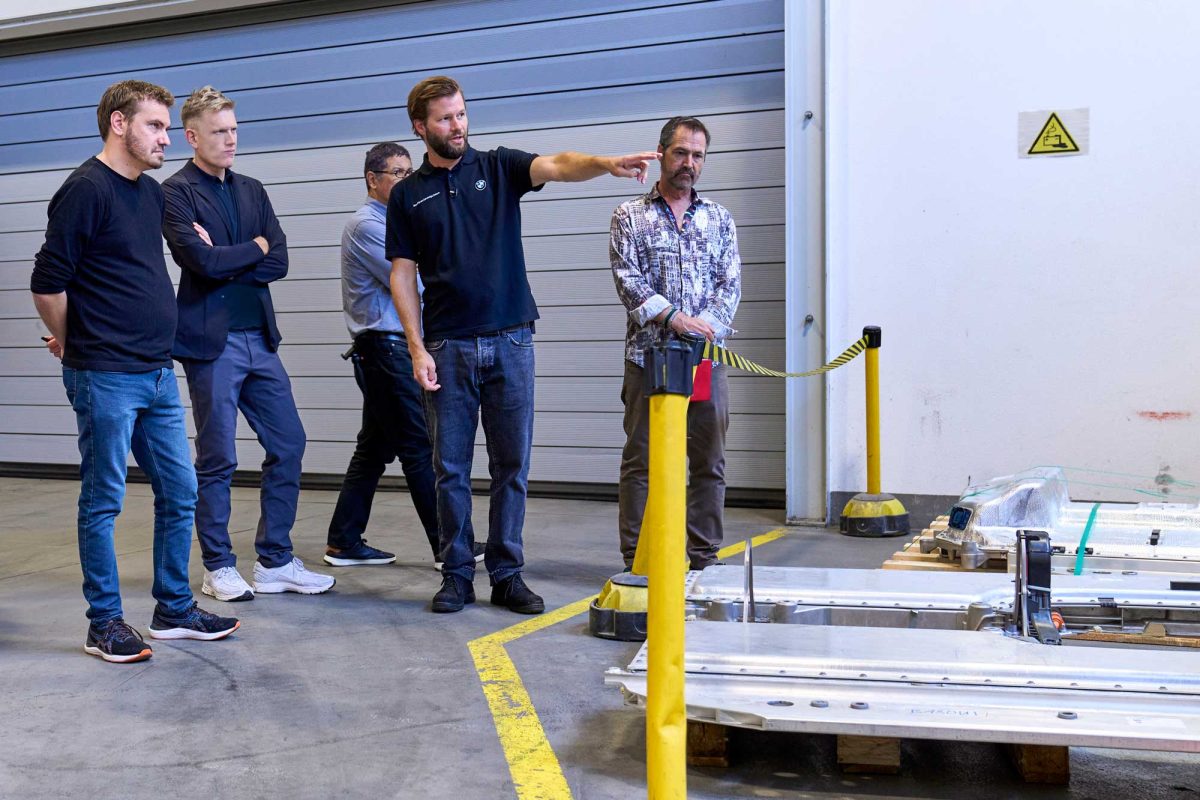

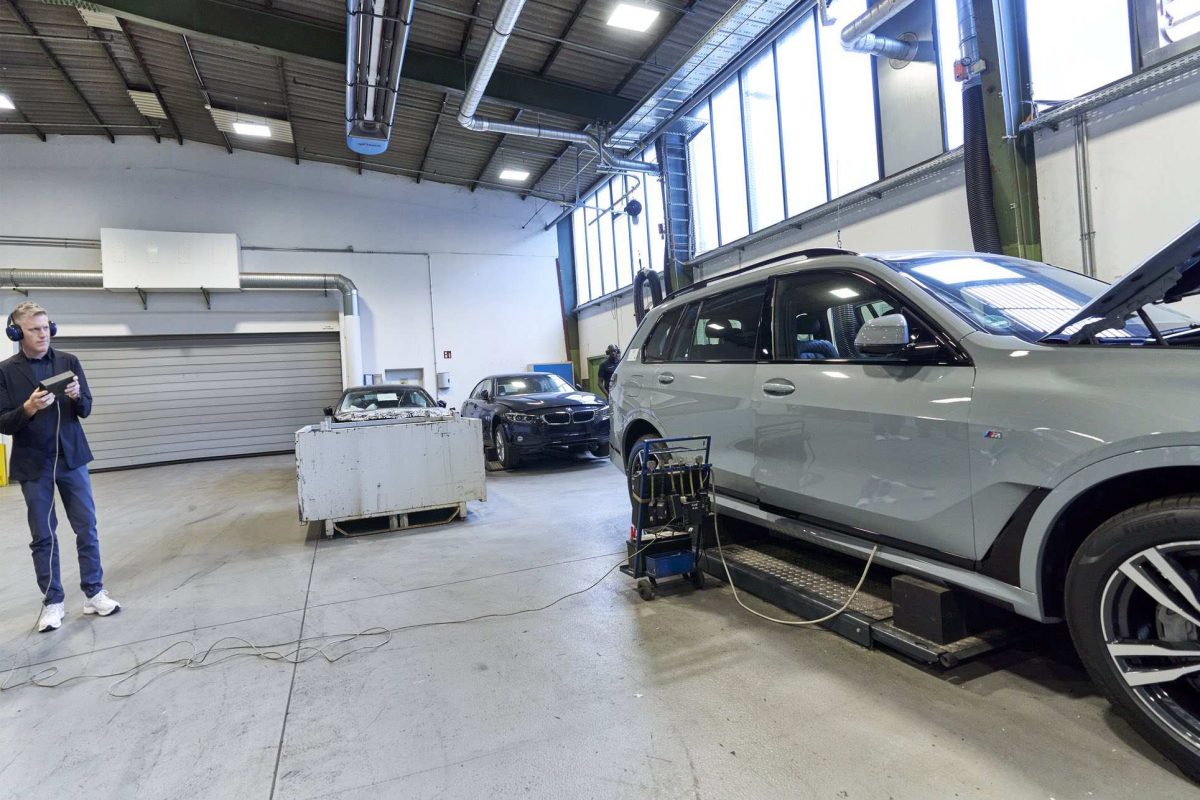



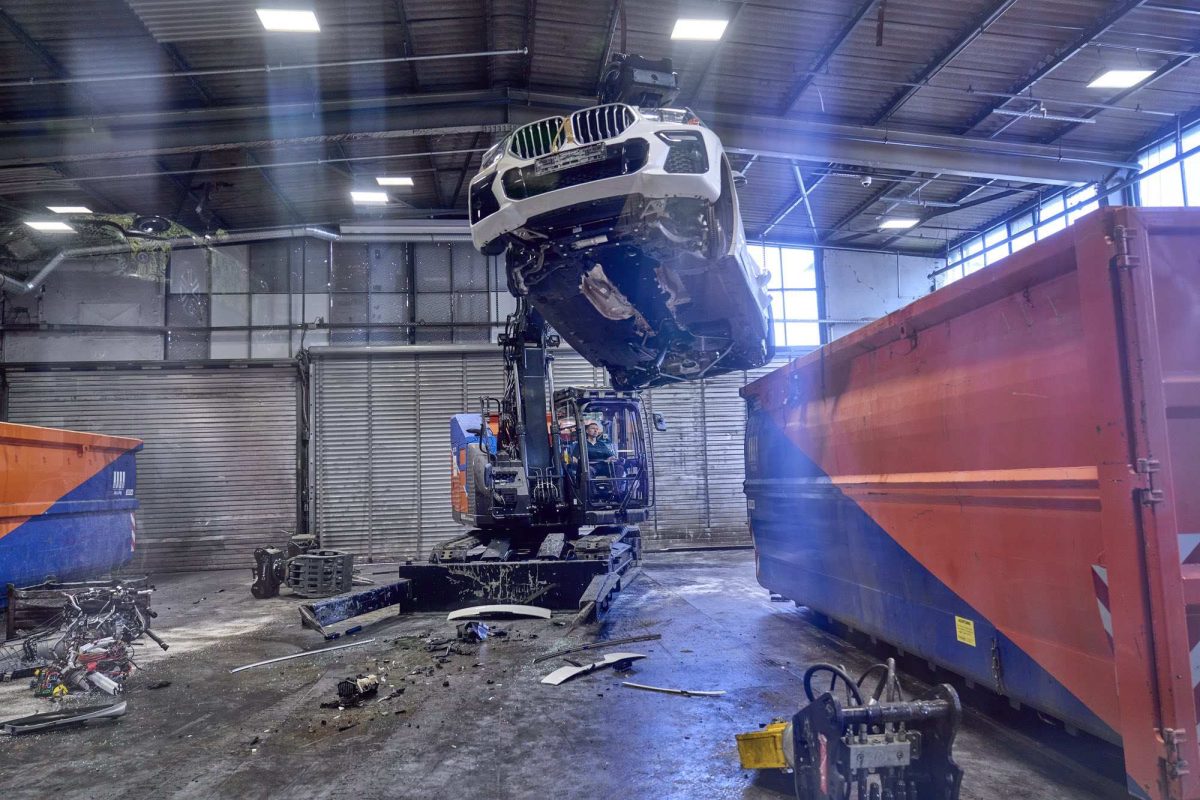

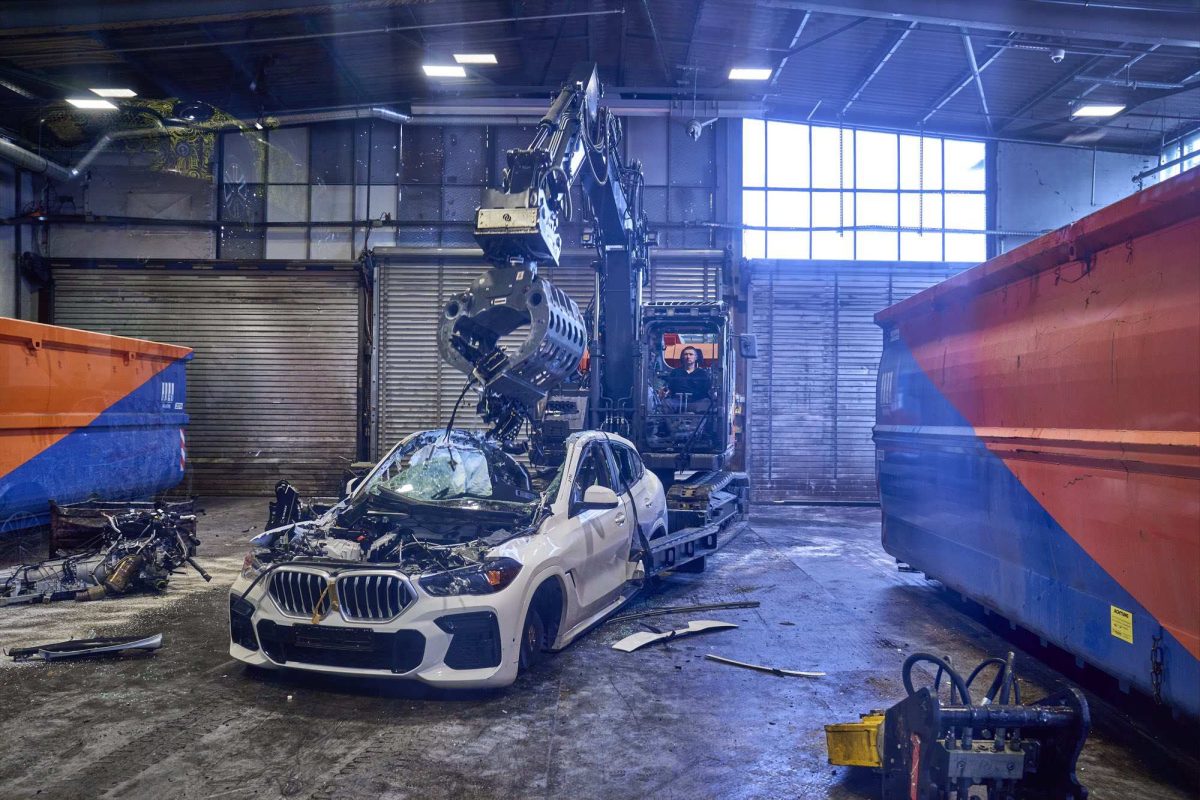


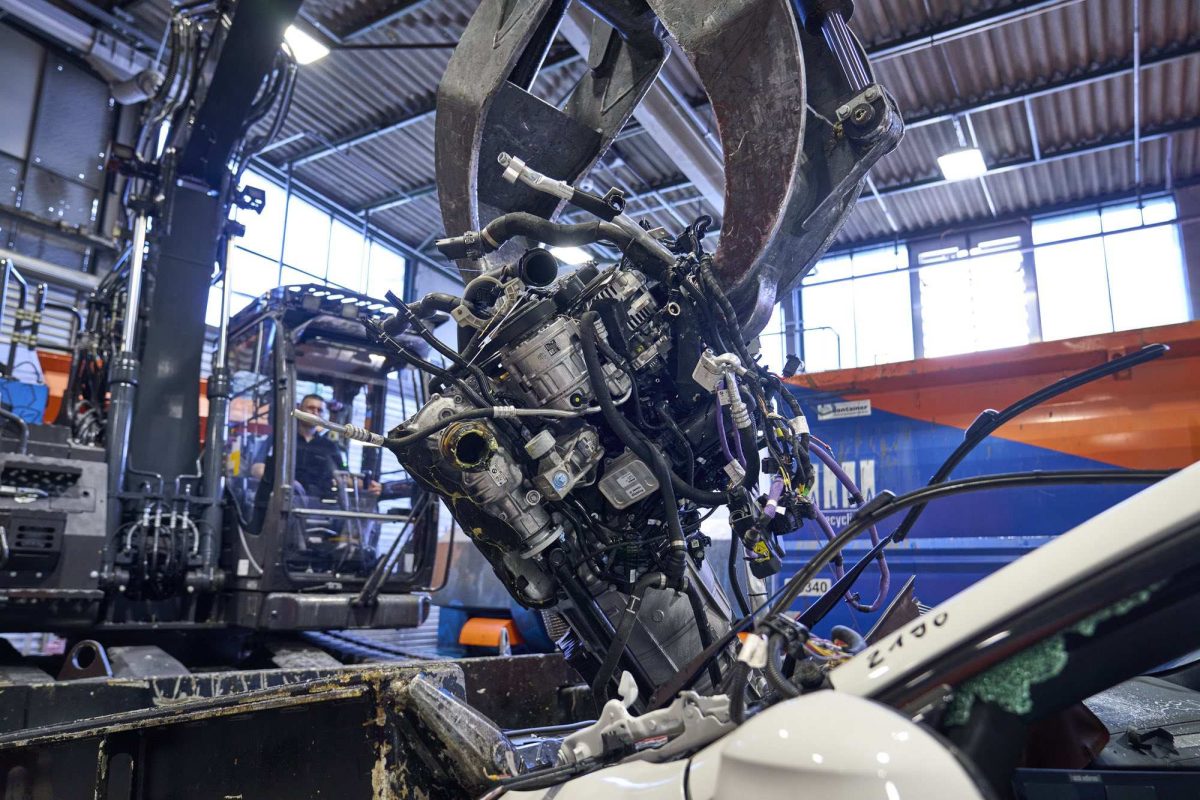
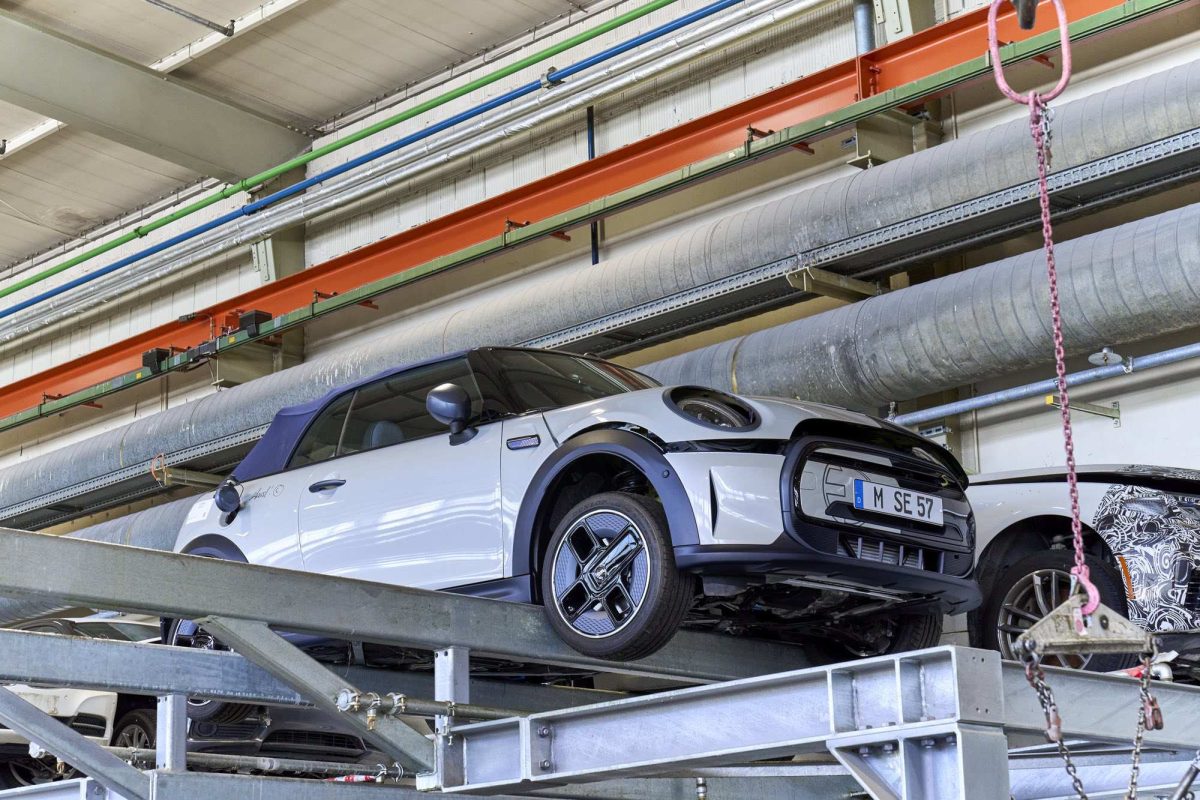






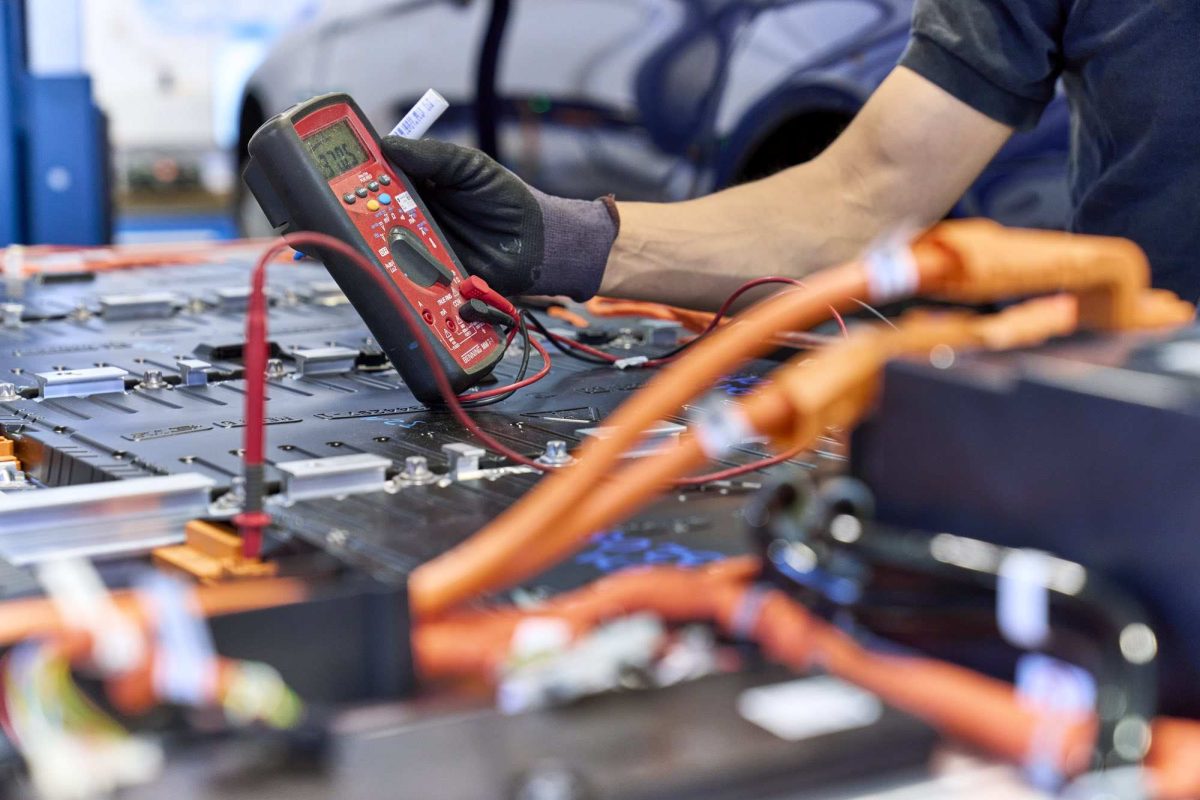
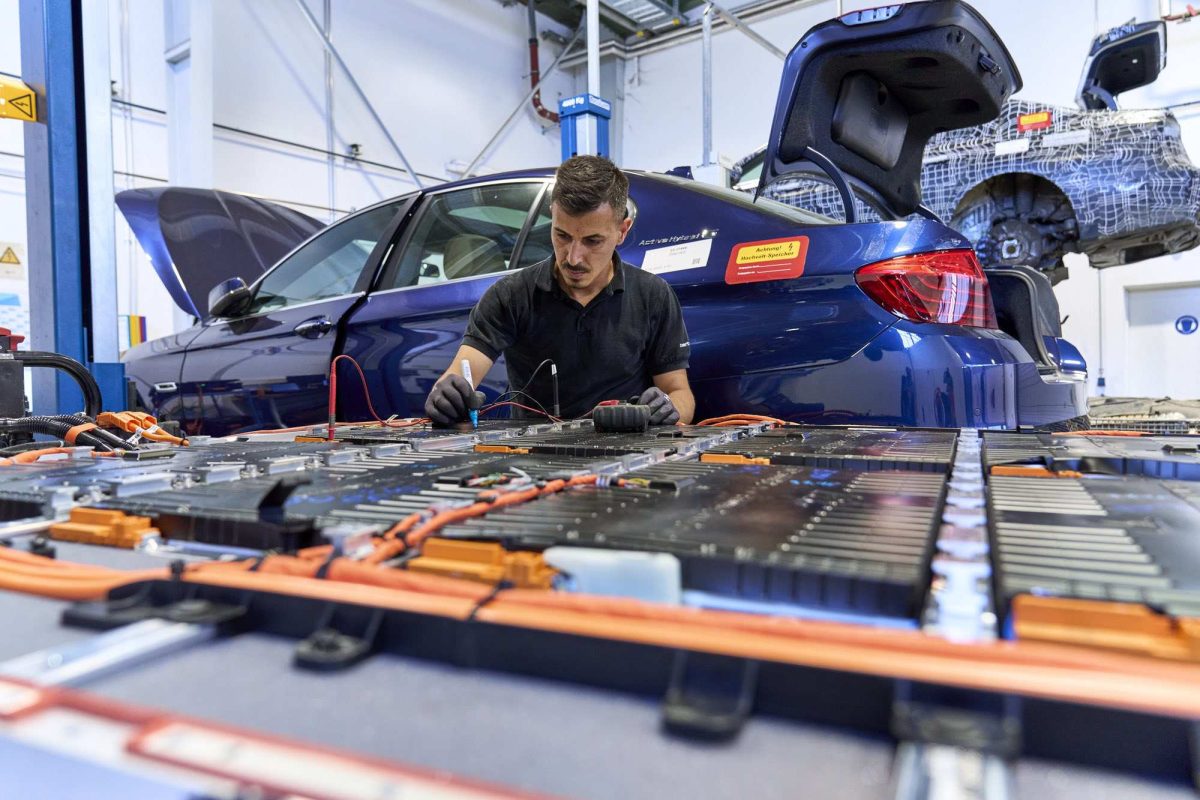








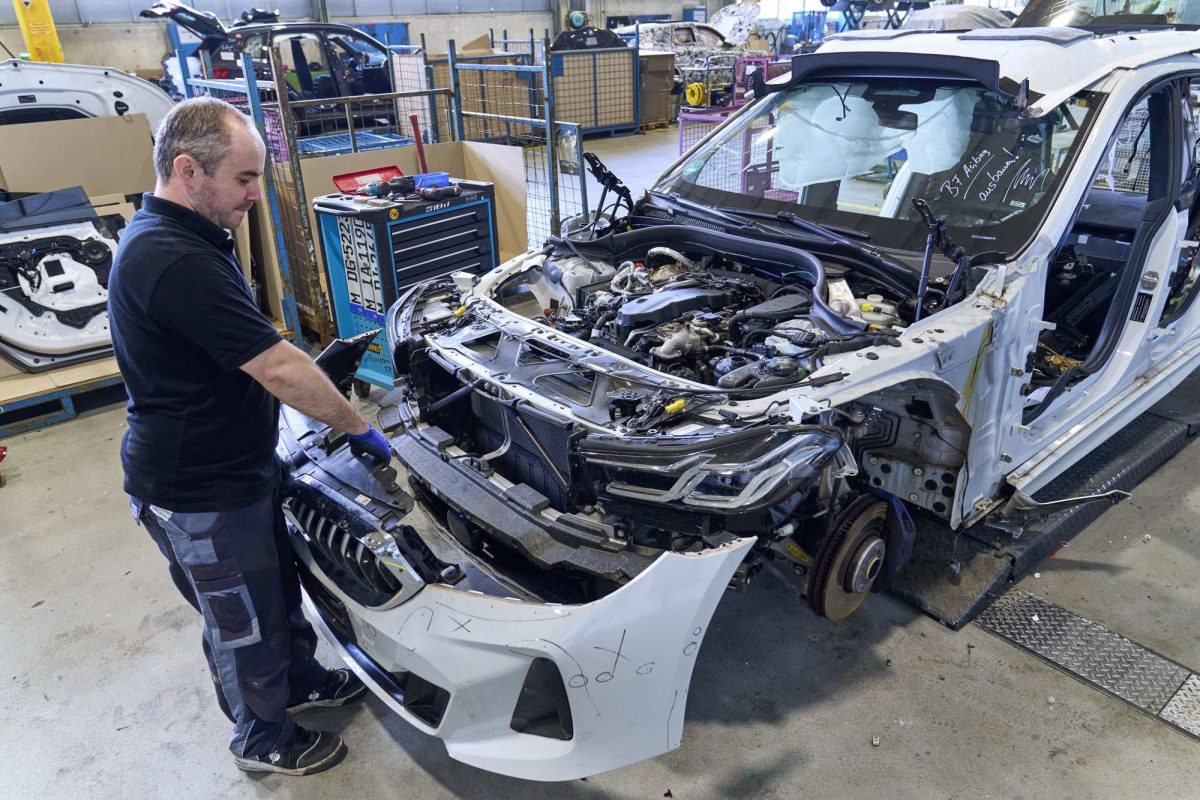

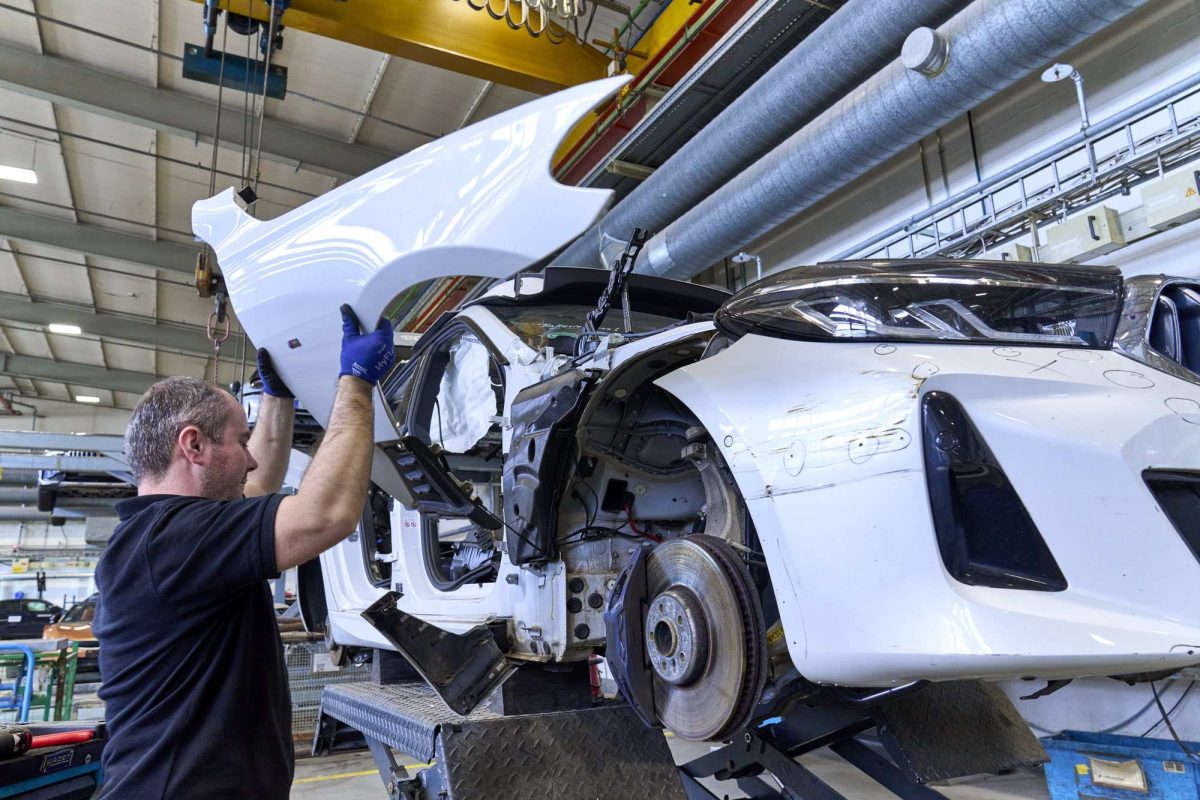




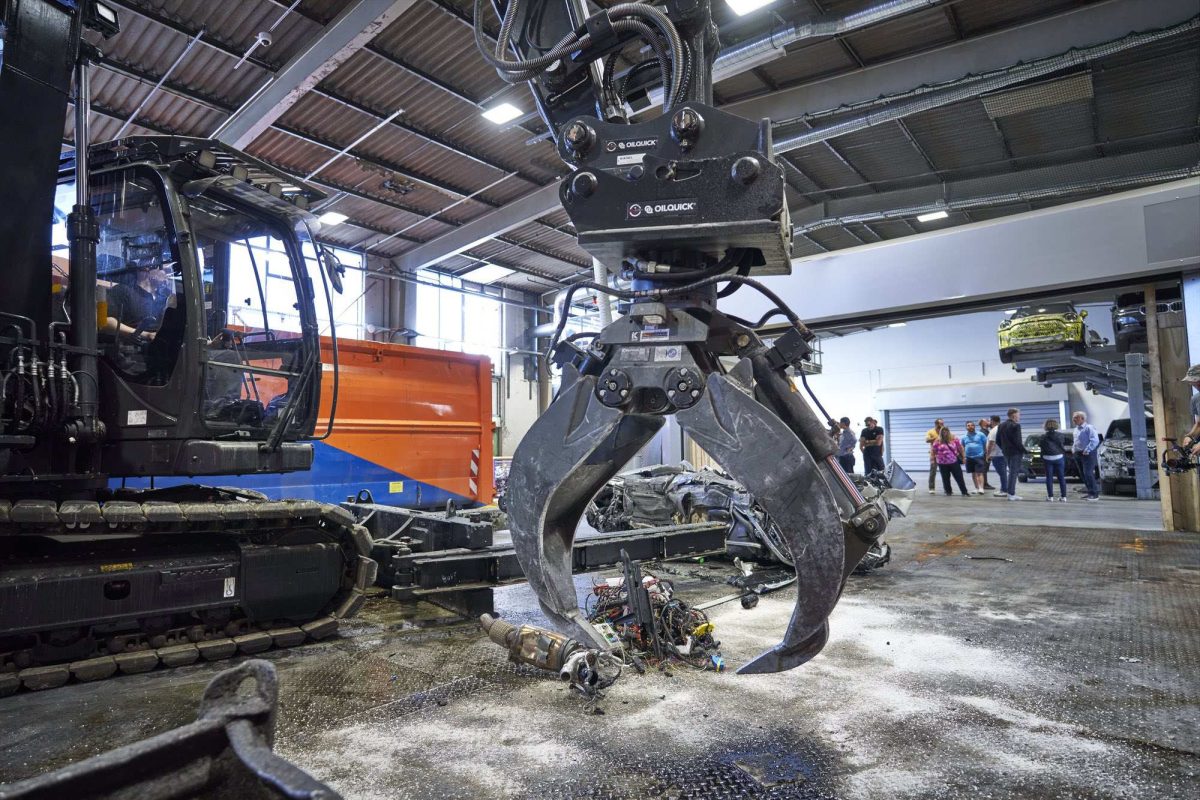

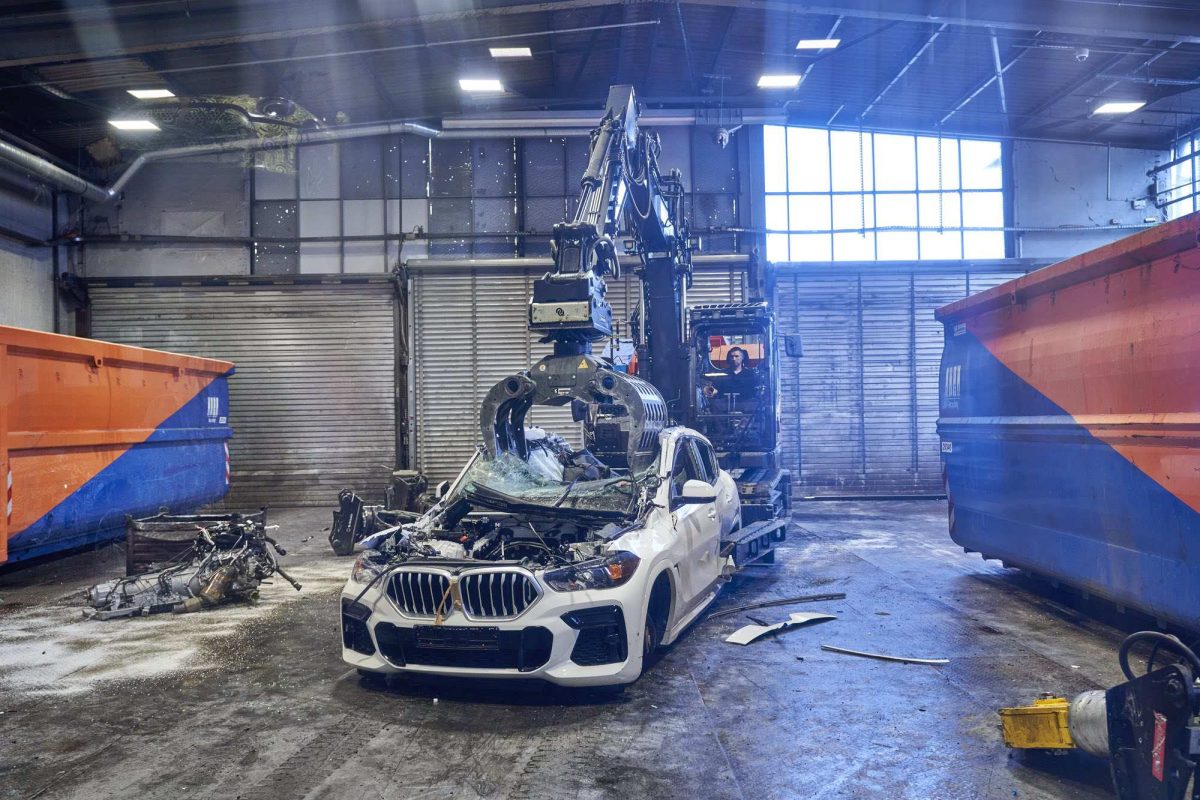
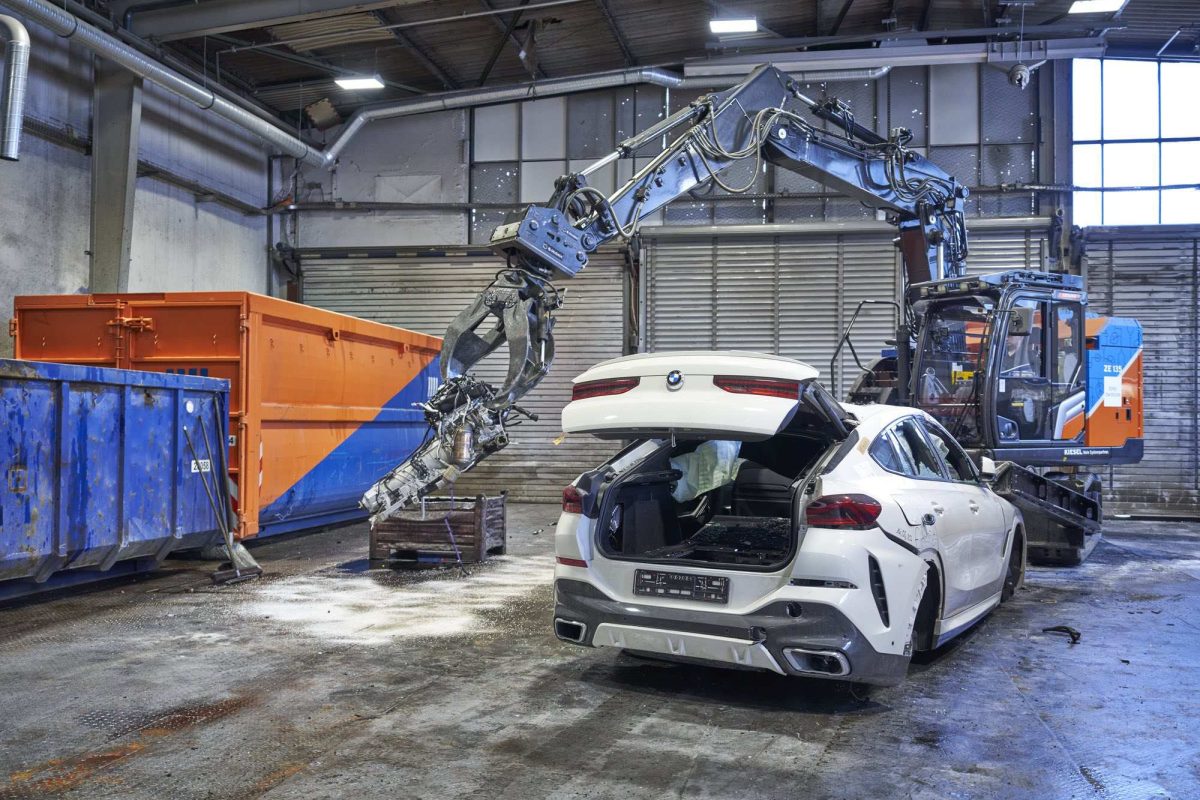



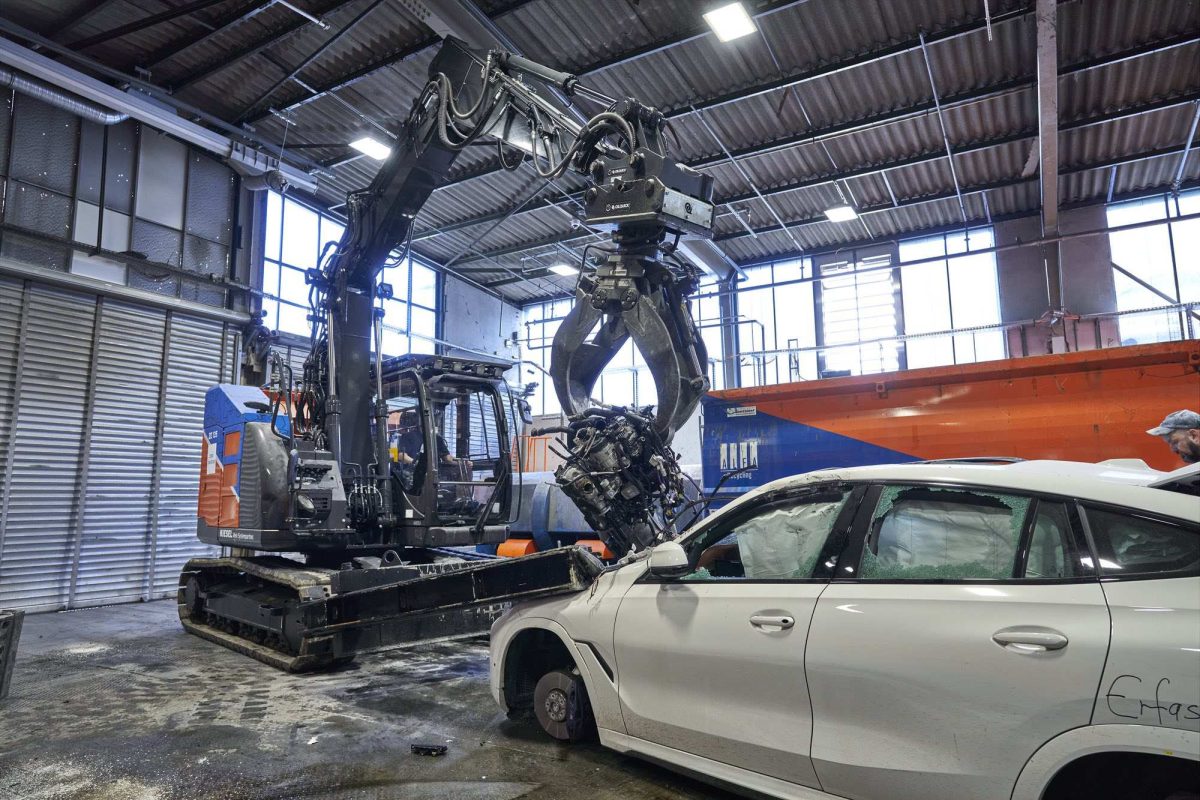

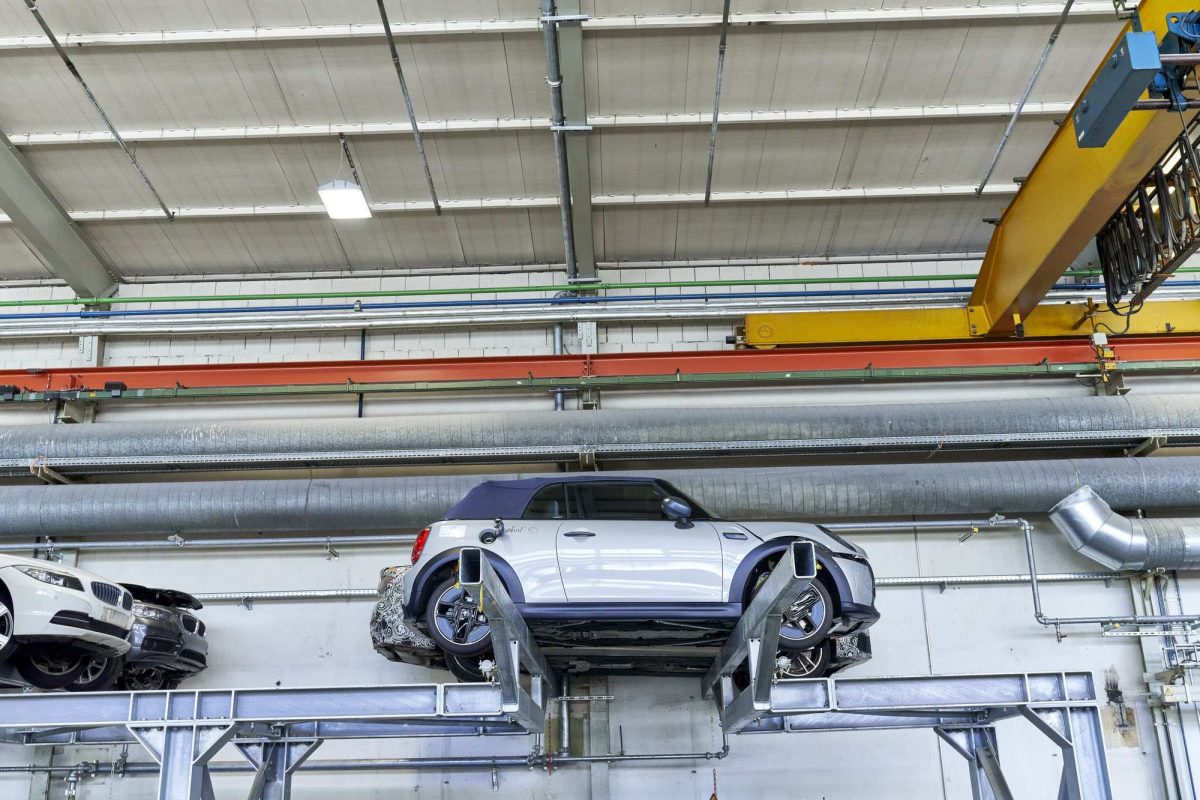


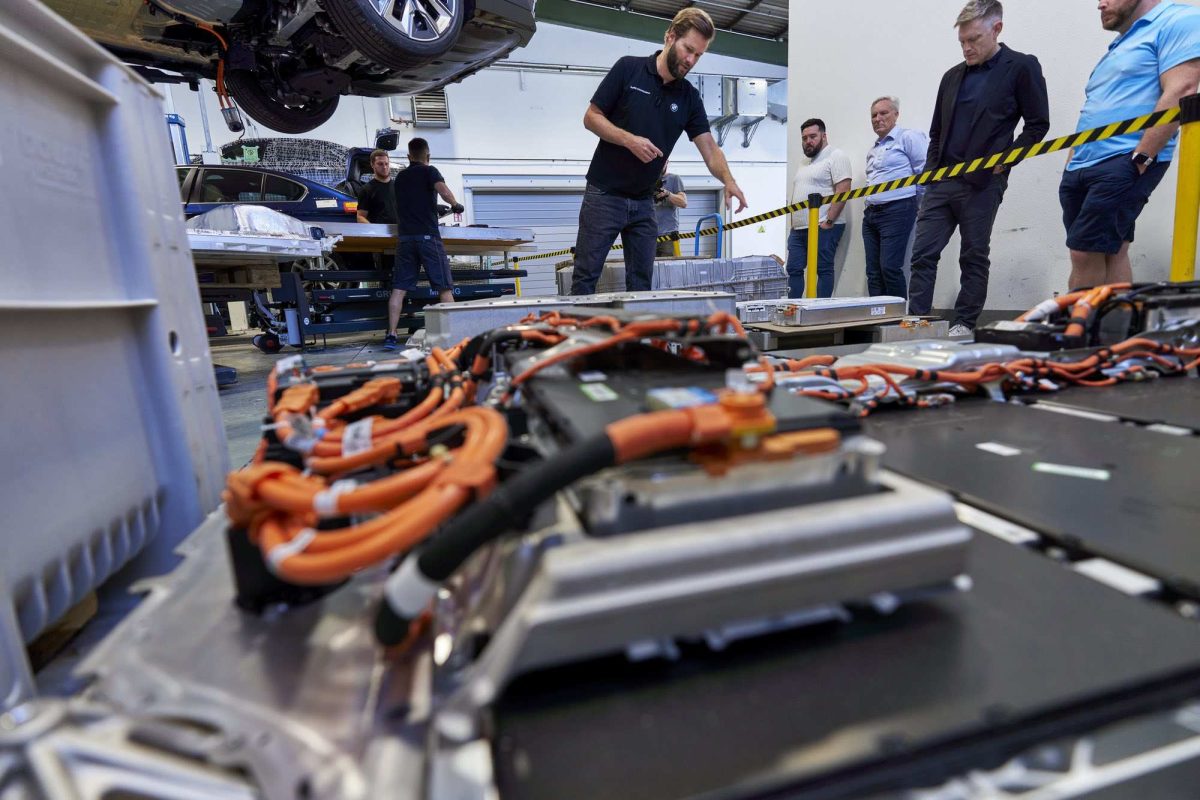









